What Is Forging?
Forging is a manufacturing process in which a metal is shaped or formed using heat, pressure, and a mold or die. The process involves heating the metal to a specific temperature, typically below its melting point, but high enough to make it malleable. The metal is then placed into a press that applies force to shape it into the desired form.The forging process requires a skilled operator who can control the temperature of the metal, the pressure of the press, and the duration of the process to achieve the desired shape with accuracy. Forging can be performed on various metals such as steel, aluminum, copper, titanium, and alloys.
Advantages of Forging
Improve strength to weight ratio
In the closed-die forging process, a metal bar or billet is heated before being placed in the mold and then hammered until the metal completely fills the mold cavity. During plastic deformation, the material's grain structure is compressed and aligned with the part shape, greatly increasing directional strength while reducing stress concentrations at corners and fillets.
Structural integrity
Forged components greatly reduce the likelihood of developing metallurgical defects such as porosity or alloy segregation that are seen in some castings. This results in reduced scrap, uniform response to heat treatment, and predictable part performance in the field.
Improved metallurgical properties
Forging can enhance the metallurgical structure of the finished part, resulting in a better-quality piece. The process can eliminate porosity, refine the grain structure, and improve the surface finish of the final product.
Flexibility
Forging is a flexible process that can produce metal parts of varying sizes and shapes with great accuracy, including complex geometries. The process can also be used to create pieces with different levels of complexity, from simple shapes to complex parts, depending on a client's specific needs.
Cost-effectiveness
Switching from solid machined parts to forged parts can save on raw material usage. Starting with a near-net-shape forging also reduces machining time. This means that companies switching from brick-and-mortar machinery to forging machinery can generate enough capacity on existing plants to save capital expenditure on new machinery as their business grows.
Reliability
Forged parts are known for being reliable and long-lasting. This is because the process creates metallurgically sound parts that are not prone to rust or breakage, making them ideal for applications where safety and reliability are essential.
-
Metal Forge
The impact of forging deforms and shapes the metal, resulting in an uninterrupted flow of crystal grains. This causes the metal to maintain its strength. -
Forged Aluminum
Forging is a manufacturing process that involves shaping metal by hammering, pressing or rolling. These compressive forces are transmitted by hammers or molds. Forging is usually class
Why Choose Us
Corporate Culture
Quality-oriented, scientific and technological innovation, scientific management, excellent products, and a good reputation—we wholeheartedly provide customers with the most satisfactory service.
Human Resources
Our existing engineering and technical staff account for 55% of our workforce. The professional management team, assisted by the company's ERP system, serves customers scientifically and efficiently in accordance with the ISO9001 system.
Our Team
We have more than 10 technical engineers, 6 drawing engineers, 8 quality inspection engineers, and 12 professional domestic and foreign sales engineers.
Our Markets
Our products are sold both domestically and internationally, particularly in North America and Europe. For example, we have customers in the United States, Canada, Germany, Switzerland, France, Italy, the Netherlands, Belgium, Poland, Spain, Ukraine, and more.
Types of Forging
Open die forging
This forging method involves the shaping of metal using a hammer or press. The metal is heated until it is soft enough to be worked with a forge hammer. This process creates a rough shape that can be further refined using other techniques.
Closed die forging
In this forging method, a die in the shape of the intended product is used to shape the metal. The metal is heated and then placed in the die, which is then closed and forged using a hammer or press. This process creates a precise shape and is commonly used to create complex parts.
Roll forging
Roll forging involves the passing of metal between two rollers to create a desired shape. The rollers are typically shaped with a specific pattern to create a specific shape or texture on the metal. This method is commonly used to create long parts, such as shafts or tubes.
Upset forging
This forging method involves increasing the diameter of a metal piece by compressing it lengthwise. The metal is heated and placed in a die, which is then upset using a hammer or press. This process is commonly used to create parts such as bolts or screws.
Press forging
Press forging involves the use of a hydraulic press to shape the metal. The metal is heated and then placed in a die, which is then compressed using the hydraulic press. This process creates a precise shape and is commonly used to create complex parts.
Isothermal forging
This forging method involves heating the metal to a specific temperature and then maintaining that temperature throughout the forging process. This method is commonly used to create parts that require high strength and accuracy.
Automotive industry
The automotive industry is one of the largest users of forged parts, specifically in the production of engines, transmissions, and suspension systems. This is because forged components are able to withstand the high stresses and temperatures that are found in these applications.
Aerospace industry
The aerospace industry also relies heavily on forging, particularly in the production of aircraft components such as landing gear, engine parts, and structural components. These are critical parts that require high levels of strength and durability, making forging an ideal manufacturing process.
Oil and Gas industry
The oil and gas industry uses forged parts in the production of drilling equipment, valves, and pipelines. These components are subjected to high pressures and temperatures, making forging a viable option due to the durability and strength of the resulting parts.
Industrial machinery
Forged parts can be found in a variety of industrial machinery, such as crane parts, turbines, and power generation equipment. These components require high strength and durability to withstand the intense forces that are generated during normal operation.
Military and defense
The military and defense industries use forged parts in a variety of applications such as weapons, armored vehicles, and aircraft. These components require high levels of strength and durability to withstand the harsh conditions of combat environments.
The main difference between forging and other manufacturing processes is that forging is a form of "hot" working while other methods such as casting, extrusion, and rolling are "cold" working methods. This means that forging involves the use of high temperatures, often over 1,000 degrees Celsius, to soften the material and allow it to be shaped more easily. Other methods, in contrast, do not involve the use of heat and rely on mechanical deformation to shape the material.Another key difference between forging and other manufacturing processes is the degree of precision that can be achieved. Forging typically yields a much higher level of accuracy and precision than other methods due to the fact that it involves the use of dies and molds. This means that the final product is likely to be closer to the desired specifications, which is especially important for high-precision applications.
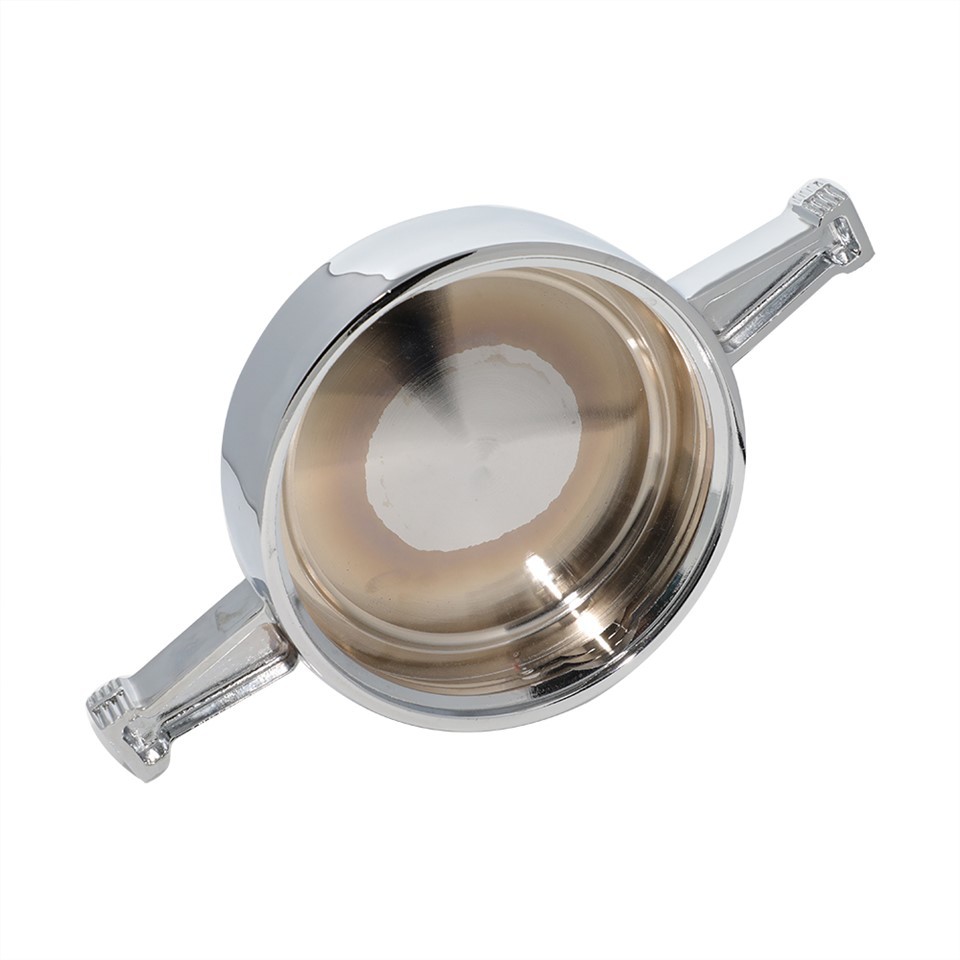
How Precise Can Forged Parts Be
Some of the benefits of producing forged parts with high precision include improved performance, increased efficiency, and extended lifespan. When parts are manufactured to exact specifications, they are less likely to fail or malfunction in service, which ultimately helps to reduce downtime and maintenance costs.
What Is the Difference Between Forging and Casting?
Forging is a method of shaping metals by subjecting them to compressive forces using a hammer, press or other mechanical equipment. The metal is heated until it is glowing red and then hammered or pressed into the desired shape. Forging is typically used for creating complex-shaped parts that require high strength, toughness, and resistance to fatigue and wear. The forged objects have improved mechanical properties, including superior strength, and the process eliminates porosity and other defects that can weaken the final product.
On the other hand, casting is the process of pouring molten metal into a mold to create a desired shape. The molten metal is typically poured into a pre-made mold, which can be made from sand, ceramics, or metal. Casting is a versatile process that can create complex shapes with fine details, making it ideal for producing decorative objects, jewelry, and sculptures. The process also offers greater design flexibility, as the molds can be easily modified or redesigned.
What Materials Are Commonly Used in Forging
Steel
Steel is one of the most commonly used materials in forging. It is strong, durable, and can be easily shaped into various forms. There are many types of steel, each with different properties, such as carbon steel, alloy steel, and stainless steel. Carbon steel is a low-cost option that is suitable for many applications, while alloy steel contains additional elements that improve its strength, hardness, and corrosion resistance. Stainless steel is also commonly used in forging as it is resistant to corrosion and staining.
Aluminum
Aluminum is a lightweight metal that is commonly used in aerospace and automotive applications. It is more expensive than steel, but it is corrosion-resistant, has a high strength-to-weight ratio, and is easily shaped into complex forms. Aluminum alloys, which contain a mixture of aluminum and other metals such as copper, magnesium, and zinc, are also commonly used in forging.
Copper
Copper is a soft, malleable metal that is commonly used in decorative applications such as jewelry and sculpture. It is also used in electrical applications due to its excellent conductivity. Copper alloys, such as brass and bronze, are also commonly used in forging due to their high strength and corrosion resistance.
Titanium
Titanium is a lightweight, high-strength metal that is commonly used in aerospace and medical applications. It is expensive and difficult to forge, but its properties make it ideal for critical components such as aircraft engine parts and medical implants.
Nickel alloys
Nickel alloys are used in harsh environments such as chemical processing, power generation, and aerospace applications. They have excellent resistance to corrosion, high-temperature strength, and are easy to forge.
Raw materials
The raw materials used in forging are metal alloys such as aluminum, copper, titanium, and stainless steel. These metal alloys are chosen based on their unique properties such as strength, durability, malleability, and resistance to wear and tear.
Equipment
The equipment used in forging varies depending on the specific type of forging process. Common types of forging equipment include hammers, presses, and rollers. Each piece of equipment is designed to apply a specific amount of pressure to the material being forged. The use of high-quality equipment is critical to the overall success of the forging process.
Dies
Dies are used to shape the metal into the desired shape. They are made from durable materials such as steel and have a specific shape and size based on the desired outcome. The dies are designed to withstand high-pressure applications and provide the necessary support needed during the forging process.
Lubricants
Lubricants are essential components of the forging process. They are used to reduce friction between the metal and the dies, which can damage the equipment and produce an inferior product. Lubricants also help to cool the metal during the forging process.
Heat
Heat is applied to the metal to make it easier to shape. The amount of heat applied depends on the specific type of metal and the desired outcome. Heat is usually applied using a heating furnace or other heating equipment.
What Are the Safety Precautions for Forging
Wear appropriate personal protective equipment (PPE)
When forging, you should wear gloves, eye protection, hearing protection, and appropriate clothing to protect yourself from sparks, heat, and debris. Additionally, you should wear respirators or masks to avoid inhaling metal fumes and other hazardous substances.
Keep the workspace clean and organized
Before starting the forging process, you should make sure that the workspace is clear of debris, oil, and other materials that may cause slips or falls. You should also ensure that all tools and equipment are in good condition and properly stored.
Use proper equipment and tools
You should use only the appropriate tools and equipment for the task. Do not use tools that are damaged or worn out, as they may malfunction and cause accidents. Also, use tools that are designed for the job, such as hammers, tongs, and anvils.
Avoid overheating the materials
Overheating the materials can cause them to become brittle and prone to cracking or breaking. Therefore, you should take care to heat the materials to the appropriate temperature and to avoid overheating them.
Use caution when handling hot materials
Hot materials are a significant hazard in forging. You should take care when handling hot materials and use tongs or other tools to avoid direct contact with the metal. Additionally, you should have a heat-resistant area to place the hot material for cooling.
Avoid working alone
Forging can be a hazardous activity, and it is best to have a partner or team member present in case of an emergency. Also, the buddy helps you to monitor the situation and makes the forging process more efficient.
How to Maintain Forging
Proper lubrication
Lubrication is essential for the maintenance of forgings as it reduces friction between the metal surfaces, prevents wear and tear, and extends the life of the parts. Applying the right lubricant to the metal parts after forging can improve their durability and reduce the risk of corrosion and other damage.
Cleaning and inspection
Keep your forging clean and dry to avoid rusting and other damages. Conduct regular inspections to check for any cracks, dents, or other defects. Any damaged parts should be immediately replaced to avoid any further damage to the forging.
Heat treatment
Many forgings undergo heat treatment to improve their strength and durability. Proper heat treatment is essential, and failure to do so can lead to a loss of hardness, which can decrease the part's strength. Therefore, proper heat treatment practices should be followed, such as using the right temperature, cooling methods, and time intervals.
Handling and storage
Improper handling and storage of forgings can damage them, leading to cracks and other defects. Ensure forgings are not subjected to excessive wear or vibration during transportation, handling, and storage. Always place them in boxes to protect them and ensure that they are stored in a dry, cool place away from sunlight.
Reconditioning
Sometimes, forgings suffer damages during use, and the condition affects its performance. When this happens, you need to recondition the metal parts or perform some repair works to restore their functionality. Reconditioning can help prevent further damage to the parts and save you the cost of buying new components.
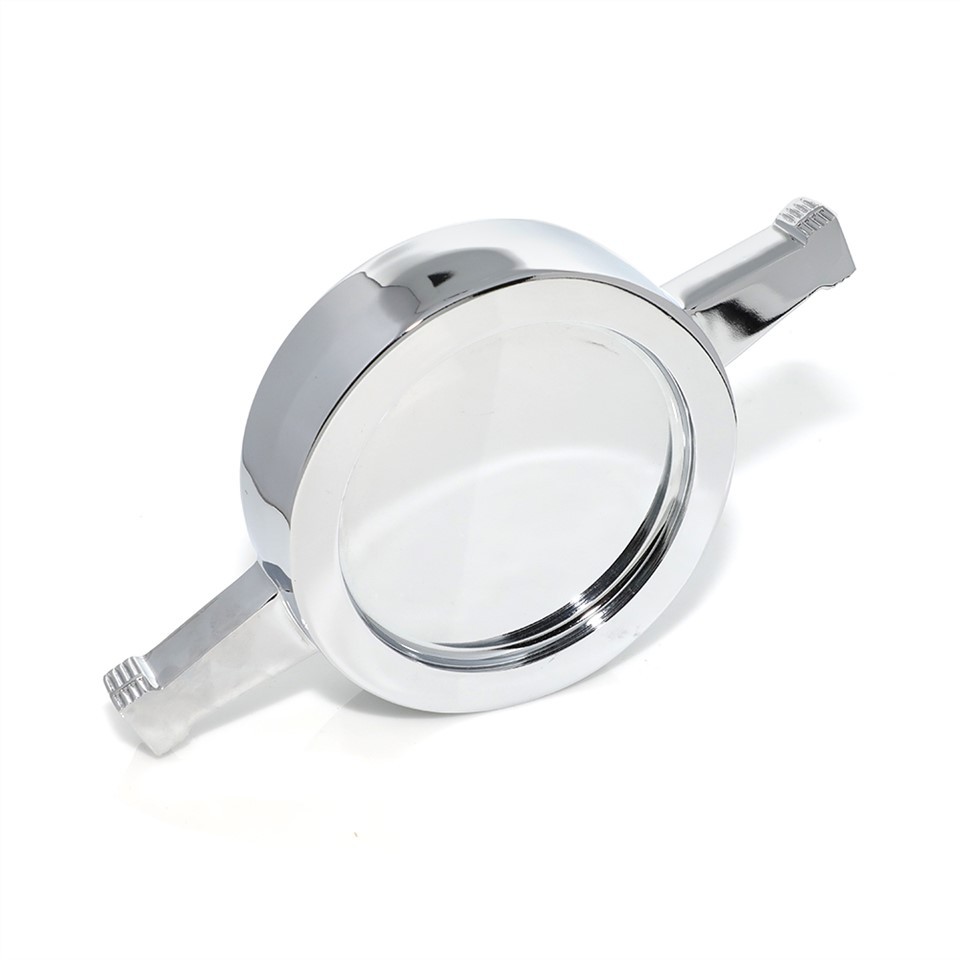
The first step in forging is to select the right type of metal for the object that you want to create. You need to choose a metal that is strong enough to withstand the forces that it will be subjected to, such as heat, stress, and impact.Once you have selected the metal, you need to heat it in a forge. The forge is a furnace that is designed to heat metal to a high temperature so that it can be shaped with a hammer or press. Most forges use coal or gas to produce intense heat, and the metal is placed inside the forge until it reaches the appropriate temperature.Once the metal has reached the right temperature, it is removed from the forge and placed on an anvil. The anvil is a large, heavy metal block that is used as a base for hammering or pressing the metal into shape. The blacksmith then uses various tools such as hammers, tongs, and chisels to shape the metal according to the desired design.During the forging process, the metal is repeatedly hammered or pressed to make it stronger and denser. This process is called "working the metal," and it involves striking the metal at different angles to create the desired shape and texture.As the metal cools, it becomes harder and more durable. The final step in the forging process is to cool the metal slowly, which helps to prevent it from cracking or breaking. Once the metal has cooled completely, it is cleaned and polished to give it a smooth, shiny finish.
Operating procedures
Before performing forging operations, detailed operating procedures should be developed, including safe operating steps, safety precautions, etc. Operators need to receive professional training, be familiar with operating procedures, and operate in strict accordance with the procedures.
Protective facilities
Forging equipment should be equipped with complete protective facilities, such as protective covers, protective fences, protective gloves, protective shoes, etc. These facilities can effectively reduce the operator's contact with dangerous parts and prevent accidental injuries.
Warning signs
Obvious warning signs should be set around the forging equipment to remind operators to pay attention to safety matters, such as prohibiting entry by non-operators and prohibiting maintenance while the equipment is running.
Safety inspection
Conduct safety inspections on Forging equipment regularly to ensure that the safety performance of the equipment meets standard requirements. The inspection content includes the equipment’s safety devices, electrical systems, hydraulic systems, etc.
Emergency measures
Develop corresponding emergency measures for possible unexpected situations, such as fire, mechanical failure, etc. Emergency measures should be concise and easy to understand, allowing operators to respond quickly.